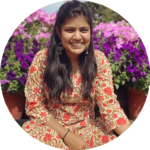
From constantly buzzing cosmopolitan cities to quaint remote towns and villages, one technology is revolutionising our lives. From making virtual meetings with participants from all corners of the world possible to powering weather-predicting supercomputers and hypersonic aircrafts, all of it is dependent on one micro-sized piece of technology: semiconductors. If a list of the most critical inputs in today’s modern information age is made, semiconductor chips will definitely feature somewhere on the top. It is these items which are credited with making all our digital gadgets “smart”. They not only have a bearing on the current existing technology but are the fuel behind the next-gen inventions too. They hold the potential to transform entire industries, from aerospace to medical diagnostics.
These chips, also called integrated circuits (ICs) are made from substances such as silicone, which are tweaked to induce changes in their conductivity. Silicon feeds a nearly 500 billion USD chip industry which is the foundation of a 3 trillion USD global tech economy.¹ The manufacturing of semiconductors is extremely resource-intensive requiring billions of investment, an uninterrupted power supply and gallons of water. These huge input demands have not however been a restricting factor to the growth of this industry. Rather, the use and application of Semicon chips have grown exponentially since 1947 when the first chip was made.² In 1965, Gordon E. Moore, co-founder of Intel observed that the size of transistors on integrated circuits doubles every two years and the cost of computers and gadgets falls.³ It has nearly been 60 years since then and that observation has now virtually become a law. There has been a phenomenal rise in Semicon chips production and a gamut of industries have come to be linked with it. However, it was only in 2021 when the shortages started occurring, factories closed down and workers furloughed that the industry found itself in an unaccustomed spotlight.
What led to the crunch?
Semiconductor chips are the brains of modern electronics and a shortage in production is bound to send shockwaves across multiple sectors. This fear has come to reality recently, and the reasons for the same have been discussed here. First, geopolitical tensions that rattled global supply chains in 2019, even before the pandemic, adversely affected this industry. The US-China trade war had a direct bearing on it. For example, Huawei which was leading the 5G project in the world was blacklisted by the US Commerce Department to prevent it from resourcing ICs without a special license.⁴ Leading producers Taiwan and South Korea, being US allies felt pulled in different directions when they were asked to boycott China, being heavily dependent on the latter for crucial imports.
Second, a demand-supply mismatch was created with the onset of the pandemic in 2020. Economists refer to the situation as the “bullwhip effect”, where small retail level demand fluctuations have larger disruption at the wholesale and manufacturing level in a supply chain. As the lockdowns came about, there was a reduction in inventories by automobile firms as the vehicle sales plummeted. Simultaneously, demand for electronic goods like PCs, laptops, and webcams rose as work from home became the norm. These two changes lead to a shift in production lines from auto to other applications, leading to a fall in the availability of auto chips when demand increased much more than anticipated. Third, a series of separate events hit different plants all across the world affecting supply. A fire broke out in Japan’s Renesas Electronics Corp., a drought occurred in Taiwan leading to a water crisis and abnormally cold temperatures in Texas lead to power outages aggravating the shortage. Fourth, and the most recent one is the precarious global economic conditions which are prevailing today due to the Russian offensive against Ukraine. 40% of palladium supplies come from Russia and Ukraine produces 70% of neon gas. Both these inputs are crucial for manufacturing ICs, and the war has created bottlenecks in their supply. Manufacturers had started building inventories after the 2014 Crimean annexation by Russia but even those are getting exhausted now. If they cannot source it from other parts of the world, the existing problem will continue to get exacerbated.
Manifestation of the shortage
The criticality of semiconductor chips is both its advantage and its massive drawback. It takes minutes to make a smartphone, and hours to make a car but it takes 4 months to make one microchip. The silicon process is so complex that it cannot be sped up, highlighting the physical limits to Semicon chip production. A gap in production cannot be filled up overnight. Thus, any shortage or disruption in production continues and manifests itself in different ways. As per a Bloomberg report, the chip lead times (time period between placing an order and delivery) increased from 6 weeks in July 2021 to 21 weeks in September 2021, going beyond 30 weeks in February 2022.⁶ As demand exceeds supply, there is an inevitable price rise. As wafer (thin semiconductor slices) prices rise, it feeds into the prices of goods which use it as an input leading to overall inflation. Automobile prices have risen by 20% in the US. The automobile industry became the worst hit due to this shortage facing a revenue loss of $110 bn in 2021. It was already facing a fall in demand even before Covid 19 and the subsequent chip crunch led to a reduction in inventories and huge cuts in production. Maruti Suzuki reported that it had to reduce production by 60% in September 2021.⁸ There has been a rise in demand for second-hand cars, with prices reported to have doubled. The electronics industry also saw a severe supply constraint which hurt the sales of laptops, tablets, and smartphones despite the rise in demand.
There are other challenges that flag the given industry. Amongst them, the number one pertaining to this discussion is that it is highly concentrated in a few geographies, in a few countries. This makes the entire supply chain very vulnerable in case of even a small disruption. Taiwan’s TSMC accounts for 92% of the total chip manufacturing in the world.⁹ It has benefited from the first-mover advantage as it was set up in 1987 and enjoys generational advancements as compared to others today. Geoeconomic tensions between China and Taiwan have flared up because of this too. Despite being the leading manufacturer of electronic goods, China is heavily dependent on microchip imports and has even indulged in industrial espionage to gain a lead. The second most important player is South Korea’s Samsung dominating the manufacture of memory chips. There are US firms like Intel and Qualcomm but they are largely focused on designing and producing for their own consumption. There exist certain Chinese firms too, but their global market share is very small.
Initially, the shortage largely impacted Europe and America but it soon spread to Asian economies, including India. The Economic Survey 2021-22 reports that as of December 2022 there were 7 lakh pending orders for cars.¹⁰ Moreover, India is highly dependent on imports for semiconductor chips, so any hiccup in the supply chain has a direct effect on domestic manufacturing. Given this precarity, the Indian government announced the National Semiconductor Mission worth 10 billion USD with a Design Linked Incentives to power the development of a chip and display ecosystem.¹¹ The Scheme for Promotion of Manufacturing of Electronic Components and Semiconductors (SPECS) was also launched for a similar cause. However, if experts are to be believed, this fiscal support is minuscule as compared to the required investment for this multi-billion dollar industry. For India to actually become “atmanirbhar”, the government needs to increase its own capital investments as well as crowd-in private participation.
Much like ours, nations worldwide are taking steps to become more self-sufficient and resilient in the face of this shortage. The semiconductor industry is now being seen as a strategic imperative. The US has proposed forging a semiconductor industry alliance with Taiwan, South Korea, and Japan as a step to prevent China from gaining dominance over this critical sector.¹² As semiconductor chips form the highest imports in value terms for China, it has aimed to produce 70% of its total consumption domestically by 2025. It seems like an ambitious goal today but China is here for the long haul. The European Union passed the European Chips Act to prevent, prepare, anticipate and respond to future supply chain disruption and enable the EU’s ambition to double its current market share of semiconductor production to 20% by 2030.¹⁵
Semicon diplomacy as the way forward
While such steps are disguised as promoting “digital sovereignty” they show a tendency of building barriers against global cooperation and globalisation. The semiconductor shortage is a case in point for the pandemic’s potential to expose the vulnerabilities of global supply chains and trade patterns. Therefore, this shortage should rather be seen as an opportunity for nations to diversify supply chains and become more resilient. Instead of individual countries aiming for self-sufficiency through zero-sum competition and beggar-thy-neighbour policies, a better way to deal with supply chain vulnerabilities would be to negotiate international arrangements. For India specifically, it must work towards Semicon diplomacy. As companies move their bases out of China, it can foster bilateral and multilateral cooperation to present itself as an alternative. It is already a part of the Supply Chain Resilience Initiative with Australia and Japan as partners. It can extend this to the QUAD alliance, with Australia as a supplier of raw materials and Japan and the US acting as tech leaders. To strengthen its Act East Policy, technological exchanges with the ASEAN grouping can also be fruitful.
Amongst all these discussions about digitisation being the way forward and its impact on the global economy, we also have to ensure that the benefits of such inventions and technologies are distributed with equity in the world. This period of stress in the industry can be analysed to understand its geo-economic implications. The chips shortage affected the advanced nations much more than the rest, as seen above. This fact can also be seen as a proxy for the biased distribution of digital benefits to a certain group of nations. Only those with access to digital goods in the first place could be the most hurt! Therefore, as semiconductor technology continues to improve and more people learn digital skills, there need to be concerted efforts taken to shrink the existing digital gaps. As the nations across the world welcome 5G, and the Internet of Things embraces our lives, we not only have to build resilient supply chains but also create robust conditions for demand to be generated in all parts of the world, equally and sustainably.
Photo Source: arstechnica.com/
About The Author
Aahana Srishti is an Economics graduate from Indraprastha College for Women, University of Delhi.
References
https://www.hitachi-hightech.com/global/products/device/semiconductor/history.html
https://www.synopsys.com/glossary/what-is-moores-law.html#:~:text=Definition,as%20E%20%3D%20mc2).
https://www.reuters.com/article/us-usa-huawei-tech-idUSKCN25D1CC
https://www.bbc.com/future/bespoke/made-on-earth/how-the-chip-changed-everything/
https://thediplomat.com/2020/09/can-china-become-the-world-leader-in-semiconductors/
https://ec.europa.eu/info/strategy/priorities-2019-2024/europe-fit-digital-age/european-chips-act_en